Japan paper: World-renowned for its high quality!
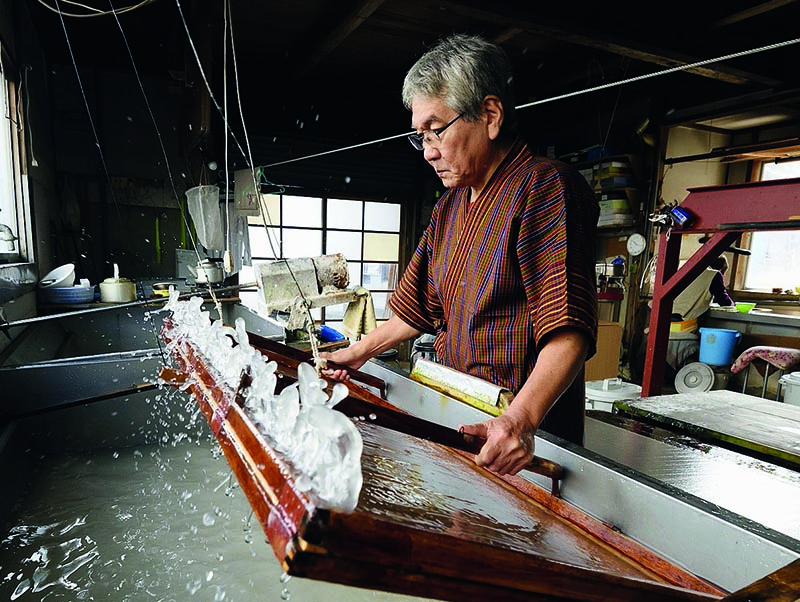
Japanese papers are mainly used for document restoration, especially for dubbing and repairing graphic works (filling gaps, consolidating tears, dubbing fragile documents) or for installing false margins to tension a document.
MORE THAN 1000 YEARS OF KNOW-HOW
Paper manufacture began in Japan at the beginning of the 7th century. Originally, paper was made from hemp, which was difficult to use due to its tough nature. Hemp was gradually replaced by fibres from native shrubs. Manufacturing techniques slowly evolved throughout the country.
The use of Kozo (mulberry tree leaves) was gradually introduced, and the strength of its long fibres made it possible to produce a paper that was both soft and strong. From generation to generation, the manufacturing technique has survived through the centuries.
Traditionally, papermaking was only seasonal. It was a matter of farmers adding Kozo to their culture. The best papers were made during the winter months, which were the months when the farmers could do nothing else. In addition, during these icy months, there were no impurities that would discolour the fibre, which often stretched out on the snow and lightened naturally. However, production was limited and did not match the ever-increasing demand.
Today, the manufacturers of WASHI (wa: Japanese; shi: paper) are building on the qualities of Japanese paper, trying to maintain ancestral traditions and keeping up with changing needs, not only at home but also around the world. Through international exhibitions, demonstrations and workshops, handmade Japanese paper is being rediscovered for its adaptability, longevity, beauty and visual appeal. As a result, the majority of art restorers use this product.
INCOMPARABLE CHARACTERISTICS
Japan paper for preventive and curative conservation is of excellent quality and traditionally hand-made by small, elite local papermakers. Made of cellulose fibres from the wood of certain varieties of shrubs, Washi are mainly produced from the species of mulberry trees. The most commonly used fibres are Kozo, Mitsumata and Gampi.
Excellent longevity
One of the main qualities of this paper is its resistance to time. It owes this longevity to the traditional methods of cooking, stack refining and drying used in its production.
Washi paper is generally pH neutral. Its condition is always good, even after more than 1000 years, and this is most certainly due to the "ingredients" that make it up.
A paper renowned for its strength
Japanese paper is particularly renowned for its strength due to its method of manufacture, the so-called "nagashi-zuki" method, which consists of interlacing long plant fibres into a uniformly strong sheet, then shaking the fibres back and forth in a mixture of water and neri or another plant with suitable sticky properties.
Then, as the fibres intertwine, the liquid is gradually wrung out with a repeated rocking motion until a regular, strong sheet of paper is produced.
THE MAIN PAPER FIBRES
The Kozo
Kozo is used in the manufacture of Japanese paper and accounts for nearly 80% of all paper used in restoration. Cultivated annually, Kozo consists of long fibres which generally results in strong and resistant papers.
Mitsumata and Gampi
Mitsumata and Gampi are rarer plant species. Mitsumata usually produces glossy, denser, very soft and noisy papers when crumpled, whereas Gampi produces fine, transparent and rather glossy papers. Depending on the treatment of the fibres, the choice of the preferred plant species and the manufacturing process itself, these characteristics may vary and the papers differ in colour (off-white, gold, light yellow, cream, etc.) as well as in thickness or texture.
HOW TO RECOGNISE QUALITY PAPER?
You should recognise the quality of a good Japanese paper by looking at :
its borders:
The edges of a sheet of Japan paper are "puffy", the sheet has not been trimmed. Hand-made paper necessarily has an excess of pulp on the edges of the sheet "made to shape".
its fibres :
Look at the paper in transparency and see the clearly visible fibres intertwined in a star shape.
its warmth :
Difficult to assess but a good quality Japanese paper feels like a warm cloth to the touch.
its natural colour:
Beware of a paper with an "intense" whiteness which may have been chemically bleached and which therefore certainly does not have a neutral PH.
LISTED AS PART OF THE INTANGIBLE CULTURAL HERITAGE OF HUMANITY (UNESCO)
Washi, traditional Japanese craft paper making skills The traditional skill of making handmade paper, or Washi, is practiced in three communities in Japan: Misumi-cho district in Hamada city, located in Shimane Prefecture; Mino city in Gifu Prefecture, and Ogawa city/ Higashi-chichibu village in Saitama Prefecture. This paper is made from the fibres of the paper mulberry tree, which are soaked in clear river water, thickened and then filtered through a bamboo screen.
Most people in the three communities play different roles in maintaining the viability of this know-how, from growing mulberry trees to teaching techniques, creating new products and promoting Washi nationally and internationally. The transmission of Washi papermaking is done at three levels: in the families of Washi artisans, in preservation associations and in local municipalities. The families and their employees work and train under the guidance of Washi masters, who have inherited the techniques from their parents.
Source: Unesco